0102030405
2100KG/2400KG Pulling Force Plywood Formwork Concrete Magnet
About Plywood Forms
Plywood forms provide a smooth finish to concrete surfaces, helping to achieve a consistent, high-quality poured surface. Plywood forms are cost-effective and can be reused many times, resulting in lower material costs than traditional wood or metal forms. Plywood formwork is waterproof and resistant to moisture, warping, rotting and splitting. And it is lightweight, easy to handle, can be easily cut and molded. Therefore, plywood formwork is favored by construction professionals.
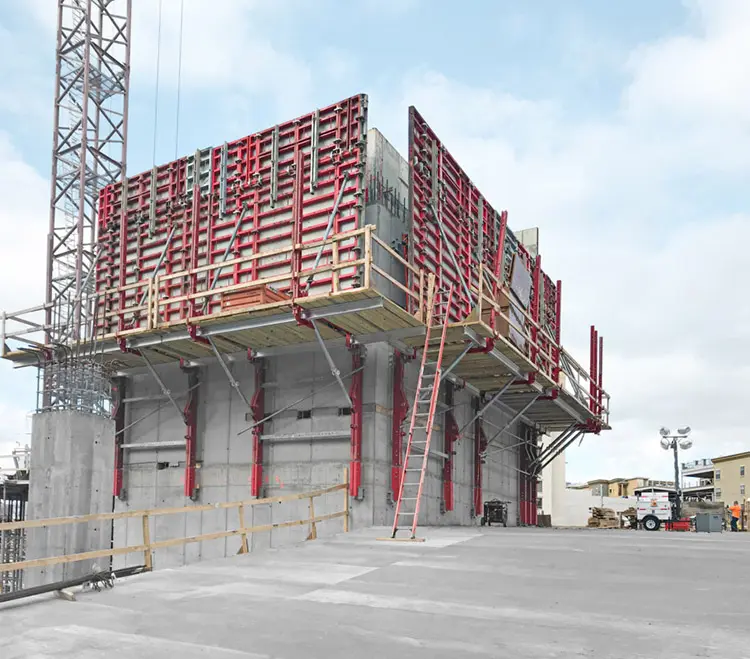
About Plywood Formwork Magnets
A Plywood Formwork Concrete Magnet is a specialized tool used in the construction of precast concrete structures. It employs magnetic technology to securely hold plywood formwork in place before the pouring of concrete, ensuring that the final product has precise dimensions and a smooth finish.
Functionality
The primary function of a plywood formwork concrete magnet is to provide a strong, adjustable hold on the formwork, which is typically made from plywood or other materials. This allows for:
- Secure Positioning: The magnet firmly attaches to steel components of the formwork, preventing movement during the concrete pouring process.
- Efficient Setup: Construction workers can quickly position and adjust the magnets without the need for additional tools, streamlining the workflow.
- Reusability: These magnets are designed for repeated use across multiple projects, making them a cost-effective solution in the long run.
Components
A typical plywood formwork concrete magnet consists of:
- Neodymium Magnet: This type of magnet provides a strong holding force, which is crucial for maintaining stability under heavy loads of wet concrete.
- Steel Housing: The magnet is encased in a durable steel structure that protects it and concentrates its magnetic force downward towards the formwork.
- Activation Mechanism: Many models feature a lever or button that allows users to engage or disengage the magnet easily. When activated, the magnet sinks and makes contact with the steel surface, creating a strong bond. To remove it, users typically need to lift a handle or use a crowbar to disengage it.
Specification
![]() |
|||||||
Model |
L(mm) |
L1(mm) |
W(mm) |
h(mm) |
M |
Weight(g) |
Breakaway(kg) |
QCM450 |
170 |
135 |
60 |
43 |
M12*30 |
1800 |
450 |
QCM600 |
170 |
142 |
60 |
43 |
M12*30 |
2500 |
600 |
QCM900 |
280 |
244 |
60 |
43 |
M12*30 |
2800 |
900 |
QCM1600 |
290 |
240 |
120 |
60 |
M16*30 |
6500 |
1600 |
QCM1800 |
320 |
270 |
120 |
60 |
M16*30 |
7200 |
1800 |
QCM2100 |
320 |
270 |
120 |
60 |
M16*30 |
7600 |
2100 |
QCM2400 |
320 |
270 |
120 |
60 |
M16*30 |
7600 |
2400 |
QCM3000 |
320 |
270 |
140 |
60 |
M16*30 |
7800 |
3000 |
Applications
Plywood formwork concrete magnets are widely used in various construction scenarios, including:
- Precast concrete production: They are widely used in precast element factories to allow rapid changes in formwork settings.
- Construction Sites: On-site use helps in forming walls and other structures with precise dimensions while reducing labor costs and improving safety by minimizing scaffolding needs.
Advantages
Using plywood formwork concrete magnets offers several benefits:
- Improved Accuracy: Ensures that concrete structures meet exact specifications.
- Increased Safety: Reduces the need for workers to perform tasks at height or in precarious positions.
- Time Efficiency: Speeds up the setup process, allowing for faster project completion.