Construction process of reserved holes and magnetic boxes of prefabricated composite panels based on BIM
2024-11-04
1.Process flow
Be familiar with and optimize the modeling of various professional drawings→→Generate a reserved plan for the composite plate components→→Introduce an infrared locator for precise positioning of the composite plate→→Install the stainless steel reserved hole magnetic box according to the positioning line→→Check and confirm the reserved holes of the composite plate→→Check the reserved holes of the finished composite plate components
2.Be familiar with and optimize the modeling of various professional drawings
Be familiar with the construction plane drawings of each profession. Under the requirements of the specifications, first optimize the two-dimensional plane drawings to make the layout of each profession beautiful and reasonable, and reflect them on the comprehensive plane drawings. Use BIM three-dimensional technology to model each profession (or directly optimize the model if the design unit has a model provided), so that each related profession can achieve a collision-free state and meet the design requirements. When checking the collision between each discipline and the floor slab, the BIM plug-in technology is used to generate floor slab reserved holes with one click, and the reserved holes that do not meet the requirements are modified in a standardized manner. For example, a DN100 pipe needs to be reserved with a DN150 casing, and the casing size is set in the model, so that the positions of the reserved holes of each discipline floor slab are finally reflected in the structural model.
3.Generate a reserved plan for composite slab components
After the model is established, the structural model floor slab is split into composite slab components, so that the reserved holes are accurately positioned on the composite slab, and the structural designer is asked to calculate the bearing capacity, so that the holes that do not meet the design specifications are reinforced, and an accurate composite slab construction plan is generated.
3D rendering of reserved holes in floor slab plan
4.Import infrared locator to accurately locate the laminated board
Generate the BIM model into the internationally accepted IFC lightweight format, import the infrared locator to locate the laminated board on the steel formwork, so that the positions of the reserved holes are reflected on the steel formwork.
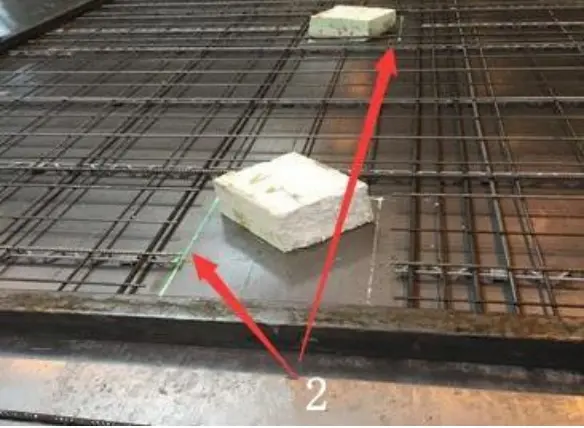
Infrared positioning
5.Install the stainless steel reserved hole magnetic box according to the positioning line
Install the stainless steel reserved hole magnetic box according to the reserved center point and line located by the partial floor drawing of the composite slab imported into the infrared positioning instrument, and fix it on the steel mold so that the reserved hole has no deviation from the design drawing, as shown in the figure below.
Fixing the steel formwork of the composite slab with shuttering magnet
6.Verification and confirmation of reserved holes of composite slabs
After the stainless steel reserved hole magnetic box on the steel formwork is positioned, the steel bars and auxiliary work are installed to complete the finished frame of the composite slab. Then, manual verification is carried out to ensure that the reserved holes on the composite slab to be cast are completely in line with the design drawings.
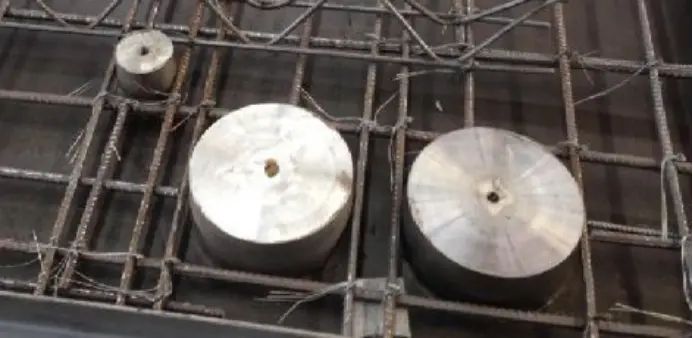
Insert magnet in the laminated slab after tying the bars
7.Checking the reserved holes of finished composite slab components
After the preparatory process of composite slab components is completed, the composite slab is cast using an automated concrete pouring machine, and then the steel mold is vibrated to make the concrete evenly and densely filled, and then moved to the curing box for curing for 8 hours. After 24 hours, the finished product is demoulded, shipped, hoisted, and installed.
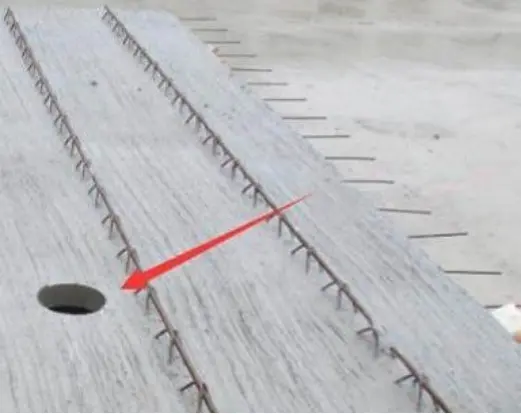
Inspection of the condition of the holes reserved after demolding of the laminated panels
Conclusion
Compared with the traditional reserved hole construction process, this construction process reduces the construction difficulty of reserved holes on the composite board, reduces the workload of reserved drawings on the construction site, improves the quality of the reservation, and avoids the situation in which the reserved holes are re-drilled on the composite board later due to the deviation of the reservation in the traditional construction process. In the process of making composite boards, the factory also reduces labor, shortens the production period, and reduces the consumption of factory materials and equipment. According to statistics for a certain project of the company, the cost can be saved by about 15%. At the same time, the reserved holes and reserved wire boxes of various specialties are constructed synchronously with prefabricated components, which reduces the workload of factory workers in pre-embedding, thereby reducing the dust, noise and other hazards caused by mechanical cutting in the factory, and has the advantages of less pollution and saving resources.