In the construction industry, the quality and stability of prefabricated components are crucial to the safety of the entire building structure. In order to improve the production efficiency and quality of prefabricated components, a new type of magnetic fixing device for prefabricated component molds for construction has come into being. This article will introduce the design features and working principle of this magnetic fixing device in detail.
Equipment structure overview
The magnetic fixing device is mainly composed of a shell, a mounting cavity, a magnet assembly, a magnetic switch, a sealing block, a soft rubber layer, a ring baffle and a limit plate. The shell is made of stainless steel plate, which is bent to form a U-shaped channel. The support plates at both ends are welded to the U-shaped channel to form a rectangular mounting cavity. This structural design is both sturdy and easy to install.
Equipment structure diagram
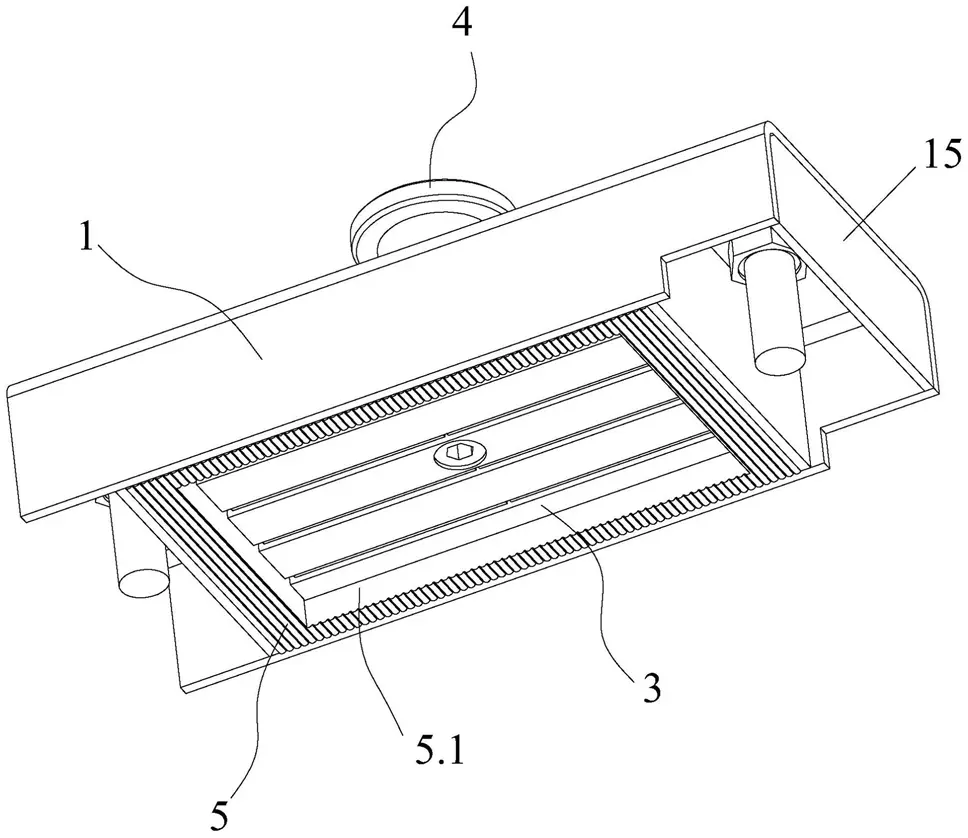
Magnet assembly and magnetic switch
The magnet assembly is the core part of the device, which is composed of multiple permanent magnets and square steel arranged in an alternating manner. Each permanent magnet is wrapped in a stainless steel ring and connected and fixed to the square steel through a threaded hole. The magnetic switch is located at the top of the housing and is magnetically fixed by driving the magnet assembly up and down.
Magnet assembly and magnetic switch diagram
Sealing and anti-mud design
In order to prevent mud from entering the installation cavity, a sealing block is provided at the opening end of the device, which is fixed by rivets or other means. The lower bottom surface of the sealing block protrudes outward from the lower bottom surface of the shell, increasing the friction between the steel platform and preventing the mold from shifting. In addition, the soft rubber layer at the bottom of the sealing block adopts a wavy structure, which further improves the sealing performance.
Optimization of magnetic performance
In order to ensure uniform and stable magnetic performance, the permanent magnets and square steels in the magnet assembly are arranged in a staggered manner, and the thickness of the square steel gradually decreases from the middle to the sides. Each permanent magnet is a two-stage structure, connected and fixed by fasteners.
Installation and limit design
The annular baffle and limit plate of the device are designed to reduce the contact area between the magnet assembly and the shell and improve the magnetic performance. The limit plate is set in the vertical direction to ensure that the magnet assembly can be stably positioned when moving up. In addition, the connection bolts and limit slots at both ends of the shell make it easy to connect the device with other components and use it with the template to improve the overall stability.
Precast concrete magnet installation diagram
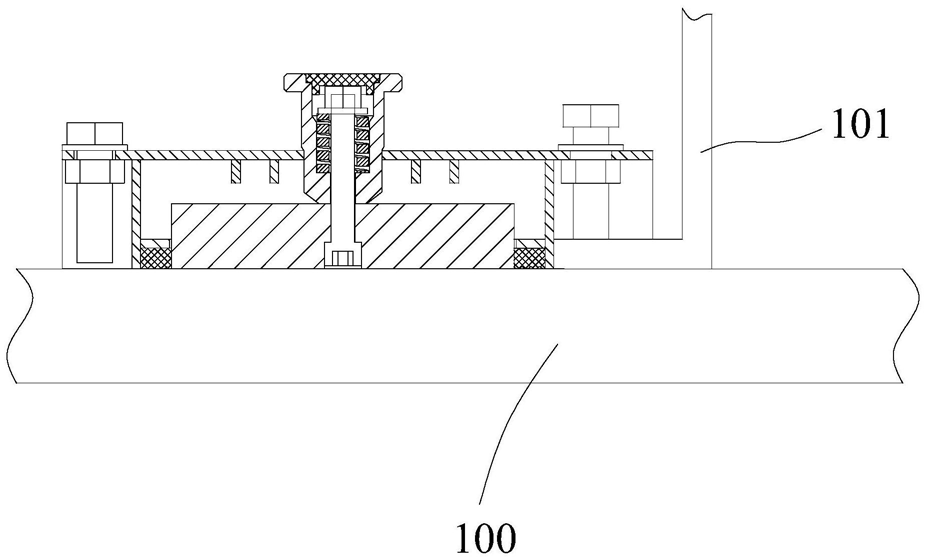
Operation and Maintenance
During operation, the magnetic switch controls the up and down movement of the magnet assembly to achieve magnetic fixation of the mold. In terms of maintenance, since the device adopts a modular design, the replacement and repair of each component are relatively simple.
Conclusion
This magnetic fixing device for prefabricated component molds for construction, with its innovative structural design and optimized magnetic properties, not only improves the production efficiency of prefabricated components, but also ensures the quality and stability of the components. Its sealing and limit design also greatly reduces the problems that may occur during the production process, which is an important advancement in mold fixing technology in the construction industry.